Damping devices
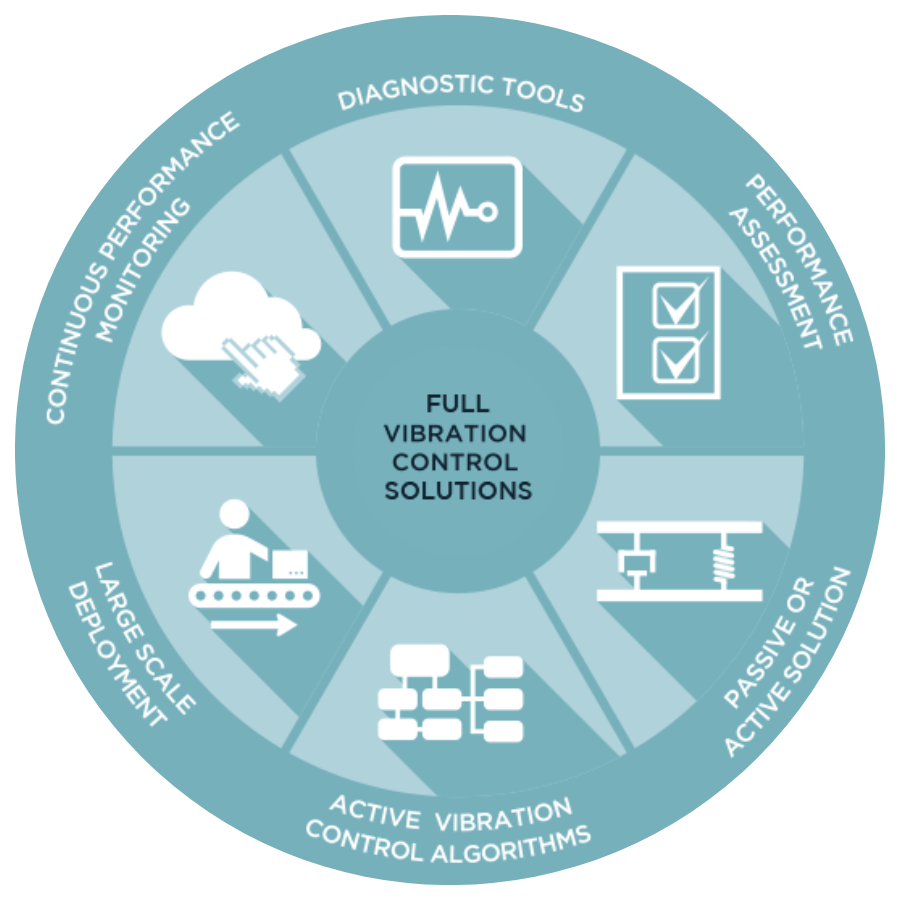
Explore Micromega Dynamics advanced vibration damping devices
Description
Due to its extensive experience in vibration control, Micromega is able to carry out analyses on the types of structural vibration and their causes, the implications on performance/reliability and how they can be reduced. With that in mind, Micromega is able to develop active and passive devices to address excessive vibration issues, even in “troubleshooting mode” where only minor modifications to the target structure are necessary.
Whenever structural vibrations are related to resonance frequencies, the structural damping should be increased.
Passive Solutions
Usually Tuned Mass Dampers (TMD) which are passive vibration reduction devices consisting of a mass, a spring, and a damper that is attached to a structure in order to reduce its dynamic response. The frequency of the damper is tuned to a particular structural frequency so that when that frequency is excited, the damper will resonate out of phase with the structural motion. Energy is dissipated by the damper inertia force acting on the structure. Adequately tuned, TMDs will replace the high peak at the structure resonance frequency by two 2 much smaller peaks. Micromega has successfully implemented TMDs in piping systems, wind turbines, semiconductor machines etc.
Active Solutions
usually Active Damping Devices (ADD) which are based on an inertial actuator and perform the same job as TMDs (e.g. increased structural damping, reduced dynamic amplification etc.) but offer enhanced performance! An ADD is also based on a spring-mass system but in this case the system is equipped with an electromagnetic force generator (i.e. voice Coil, electromagnet, motor etc.) between the static and moving part of the actuator. While, with a TMD, the spring mass frequency is tuned to the targeted resonance, in an ADD, the spring mass frequency can be chosen arbitrarily as long as it is below the first resonance frequency. In fact, an inertial actuator can be considered as a pure force generator for frequencies above its internal suspension frequency.
What we do
- Fatigue analysis of the ADD/TMA/TMD flexible components – device lifetime evaluation
- Design of magnetic damping components for optimally tuned dampers
- Material Lists for demanding environments (clean room, vacuum, nuclear plant etc.)
- Dedicated mechanical interfaces
- The design of dedicated ADD/TMD/TMA (weight, tuning frequency, available space & mechanical interfaces, thermal environment, manufacturing costs for serial implementation etc.)
- The manufacturing and commissioning of the ADD/TMA/TMD
Contact Us
You have a question ? You need a quote ?
Tel : +32 (0) 81 24 81 00 | Mail : commercial@micromega-dynamics.com