Active Damping Devices
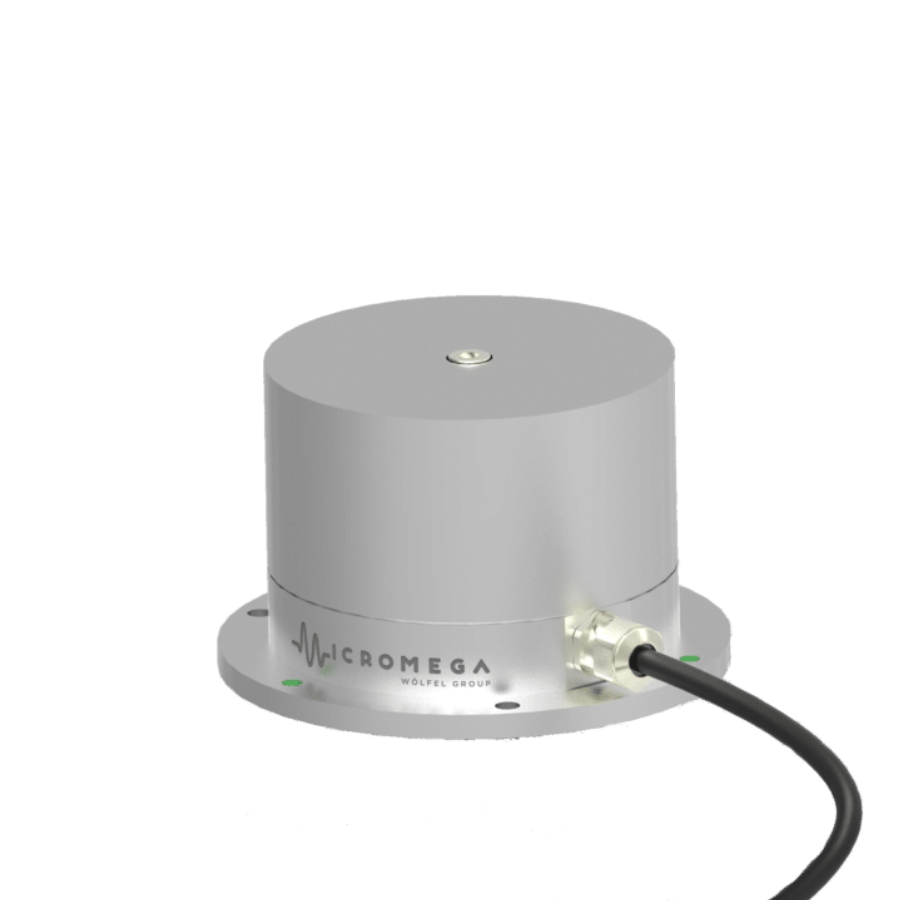
Structural Active Damping Devices
Description
Active Damping Devices, the ideal solution for enhancing the performance of highly precise and sensitive equipment, especially in applications such as structural active damping. When traditional passive or active isolation platforms fall short, and local/global resonances threaten to compromise your equipment’s precision, our Active Damping Devices step in to revolutionize your isolation system.
Whether you’re dealing with sophisticated equipment like microscopes, inspection devices, imaging systems, or polishing machines, the need for optimal performance is paramount. In scenarios where the existing isolation system lacks the required stiffness or is affected by perturbation sources on the isolated part, our Active Damping Devices provide a transformative solution.
By introducing structural active damping into unwanted mechanical resonances, these devices can achieve up to 15% structural damping without the need for major redesign efforts. Unlike passive dampers, our Active Damping Devices are lighter and remain insensitive to changes in the supporting structure dynamics.
Typical use
Structural active damping finds its stride across a spectrum of applications where precise management of dynamic forces is imperative. Here’s a glimpse into the typical use of structural active damping:
- Structural vibration reduction of isolated machines for performance improvement (microlithography, microscope, chip manufacturing or inspection machines, etc.)
- Machine tool chatter reduction
- Improved overlay of printing process
- Paper mill roll barring avoidance
We also provide Passive Damping Systems. Discover it.
Additionnal Informations
Benefits of structural active damping
The key benefits of structural active damping include:
- Vibration reduction with an ADD is a non-intrusive process. No structural modification is needed. The device does not degrade the static strength or stiffness of the target structure
- The ADD performances are not affected by changes in the resonance frequencies
- Performance with an ADD is an additive process, so the more devices you attach to the structure or machine, the more vibration reduction you get
- An ADD does not need to be tuned to the respective target resonance
- Compared to passive Tuned Mass Damper, ADD are usually lighter and better performing
- Micromega Dynamics has more than 20 years of experience in the design, manufacturing and installation of ADD
Understanding Active Dumping
Structural active damping is a technique used to mitigate or control vibrations and resonances in structures by actively introducing damping forces. Damping refers to the dissipation of energy in a vibrating system, and it’s a crucial aspect in controlling vibrations and preventing resonance-related issues.
In structural active damping, sensors are used to detect vibrations or resonances in a structure. These sensors send signals to an active damping system, which, in turn, generates forces to counteract or dampen the undesired vibrations. This is typically achieved using actuators, such as hydraulic or electromagnetic devices, that exert forces on the structure to counteract the movement caused by vibrations.
Discover our different usecases
Contact Us
You have a question ? You need a quote ?
Tel : +32 (0) 81 24 81 00 | Mail : commercial@micromega-dynamics.com